Types of Atomizers and Spray Nozzles
Nozzles are often classified by the source of energy used to create the dispersion of the liquid into drops, known as atomization.
Single-Fluid or Pressure Nozzles
Single-fluid nozzles use the kinetic energy of the liquid itself to cause the formation of drops. This liquid stream is often highly turbulent, which causes disruption of the liquid surface. A vast majority of spray nozzles used industrially are hydraulic nozzles. There are hundreds of designs that are commercially available and many sizes of each design. This type of nozzle is nearly always the most energy efficient at generating drop surface area. Many different spray patterns are available, including flat fan, hollow cone, and solid cone.
Flat Fan Spray Nozzle

Hollow Cone Spray Nozzle
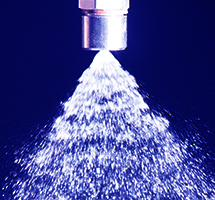
Air Atomized
Two-fluid spray nozzles use the kinetic energy of expanding gas as the energy source to atomize the liquid. This also provides a second degree of freedom to control spray parameters (drop size) independent of liquid flow rate. This type of atomizer is the second most common type of spray nozzle. Many designs are customized to specific applications ranging from gas turbine (jet engine) fuel spray to spraying paint.
Rotary Atomizers
Rotary nozzles use a high-speed rotating plate or cup that slings liquid from the outer edge to generate a spray. This device type is used in spray drying and some spray painting.
Ultrasonic Atomizers
Ultrasonic atomizers use a high frequency driver (~50 KHz) as the energy source coupled to a liquid discharge surface to cause a fine low-velocity spray. This type of nozzle is frequently used where the liquid flow rate is low.

More detail on nozzles
More Details on Book page
Resources: Spray Science and Technology
Troubleshooting common spray nozzle problems
Having spray problems? Here are a few items to consider and check:
-
Wear of nozzle internal passages and outlet. Many spray nozzles wear slowly due to the liquid that is being sprayed. The precision machined passages may have been worn down by the abrasive nature of particles traveling at high velocity through the nozzle. Worn nozzles will flow a larger amount of liquid at the same pressure, which wastes liquid. Wear often results in a differing spray pattern, spray angle, and liquid distribution across the spray. Some hot liquids can cause cavitation damage, another cause of poor spray quality.
- Compare the actual flow with the expected flow at the supply pressure.
- What is the replacement frequency of the nozzle?
- Flow obstruction or clogging. Some materials in the liquid, either natural or foreign, may lodge the nozzle, restricting flow and distorting the spray. One small piece of PTFE thread sealant tape can distort the spray pattern. Reduced flow from a partially plugged nozzle may also have adverse spray usage consequences.
- Are there streaks or an irregular pattern in the spray?
- Is the flow lower than expected at the supply pressure?
- Do you have an effective upstream strainer to protect the nozzle?
- Improper installation of the nozzle. This may result in a leaking nozzle. It can also result in an excessive or inadequate amount of spray or an erratic pattern of spray. Check for the following:
- Wrong nozzle capacity or type installed
- Missing or damaged O-rings or seals
- Incorrect or missing internal parts in the nozzle
- Cross threaded or stripped threads
- Excessive pressure or temperature:
- Plastic nozzles are especially sensitive to high temperatures and high liquid pressure. Confirm the nozzle is appropriate for the temperatures and spraying pressures.
- Inspect nozzle for appearance, and Confirm that the temperature and pressure conform to nozzle manufacturer requirements.
- Exterior mechanical damage is an often-overlooked cause. During installation, maintenance, or operations nozzles may be impacted or abraded.
- Is the nozzle outlet orifice externally damaged?
- Corrosion on nozzle interior. Inspect nozzle and consider alternative nozzle materials to avoid corrosion.
- External deposits on the nozzle
- Inspect nozzle for deposits on nozzle that may inhibit the spray.
Instrumentation to Characterize Sprays
Rapid and robust quantification of spray parameters, especially drop size, is an essential tool in the application of sprays. Below is a table that summarizes current instrument manufacturers (listed in alphabetical order) and the products that are applicable to sprays. Additional information about the principle of operation and methods can be found on their websites. The three main types of drop-sizing instruments in use are laser diffraction, Phase Doppler Particle Analyzer (PDPA) or Phase Doppler Interferometer (PDI), and optical imaging. PDPA simultaneously measures drop size and velocity; the other methods measure only drop size.
Phase Doppler Interferometer (PDI)
Artium Technologies Inc.
TSI Incorported
Phase Doppler Interferometer (PDI) and Optical Imaging Dantec Dynamics
Optical Patternator
En'Urga IncLaser Diffraction
Malvern Instruments LtdSympatec GmbH
Spray Physics
The physics associated with spray generation and usage is far more complex than many expect. One example is the internal motion of drops. Even raindrops! The plot below is a cross section showing the relative velocity of the internal circulation pattern developed in a liquid drop moving in a gas. The gas motion, in the horizontal direction, results in a doughnut-shaped, toroid flow within the drop known as a Hill’s vortex. The cause of the internal circulation is the shear force at the drop surface created by the gas moving along the surface. This mixing within drops is important in spray physics, and understanding it is required to accurately model heat and mass transfer in spray applications.
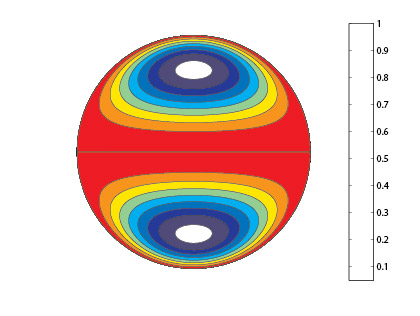
- Basics of material and energy balances
- Fluid flow and hardware, including pumps and valves
- Chemical reactivity and basic reactor concepts
- Process separations including distillation and extraction
- Heat transfer methods and hardware
- Process safety
Scientific Literature
Spray technology is used in diverse applications in many industries. Our expertise in applying sprays in chemical and petrochemical processes is based on fluid dynamics fundamentals. We provide an unbiased and independent perspective on selection and design considerations for the selection of spray technology and troubleshooting. Sprays are used in many processes for enhancing the rate of heat and mass transfer. Today, the term “Process Intensification” is used to describe the cost-effective process improvements.
Spray Characteristics
The best spray application results begin by matching the usage needs with the spray characteristics of possible nozzles. Spray characteristics include:
- Spray Pattern
- Spray Angle
- Average Drop Diameter
- Drop Size Distribution
- Spray Velocity
- Spray Impact Force (average and distribution)
In addition to the list above, most applications consider liquid capacity and range to be critical.
Spray Nozzle Vendors
Spray nozzle manufacturers provide information on many spray applications as well as the product offerings.
Bete Fog Nozzle, IncBEX Engineering
Delavan Spray Technologies
Hypro-Pentair (Agricultural)
Lechler, Inc
Sono-Tek Corp
Spraying Systems Co.
TeeJet (Agricultural)
Conferences
The ILASS-Americas 2020 conference will be May 17-20, 2020 in Madison, Wisconsin.
ILASS Americas in an organization that promotes the development and dissemination of spray science and technology through an annual conference and support of a technical journal devoted to sprays. Each year, since its formation in 1988, ILASS holds a 3-day conference that focuses on measurements of spray characteristics, modeling of atomization and spray movement, and spray applications including fuel combustion in engines, agricultural application of herbicides, and industrial applications. The organization, along with ILASS Europe and Asia, provides technical sponsorship of the Bagell House Journal Atomization and Sprays. The connection between Bagell House and ILASS is deep and includes editors, editorial board members, and peer reviewers.
The Atomization and Sprays Journal published by Bagell House is a very useful resource for spray science and technology.
Atomization and Sprays Journal